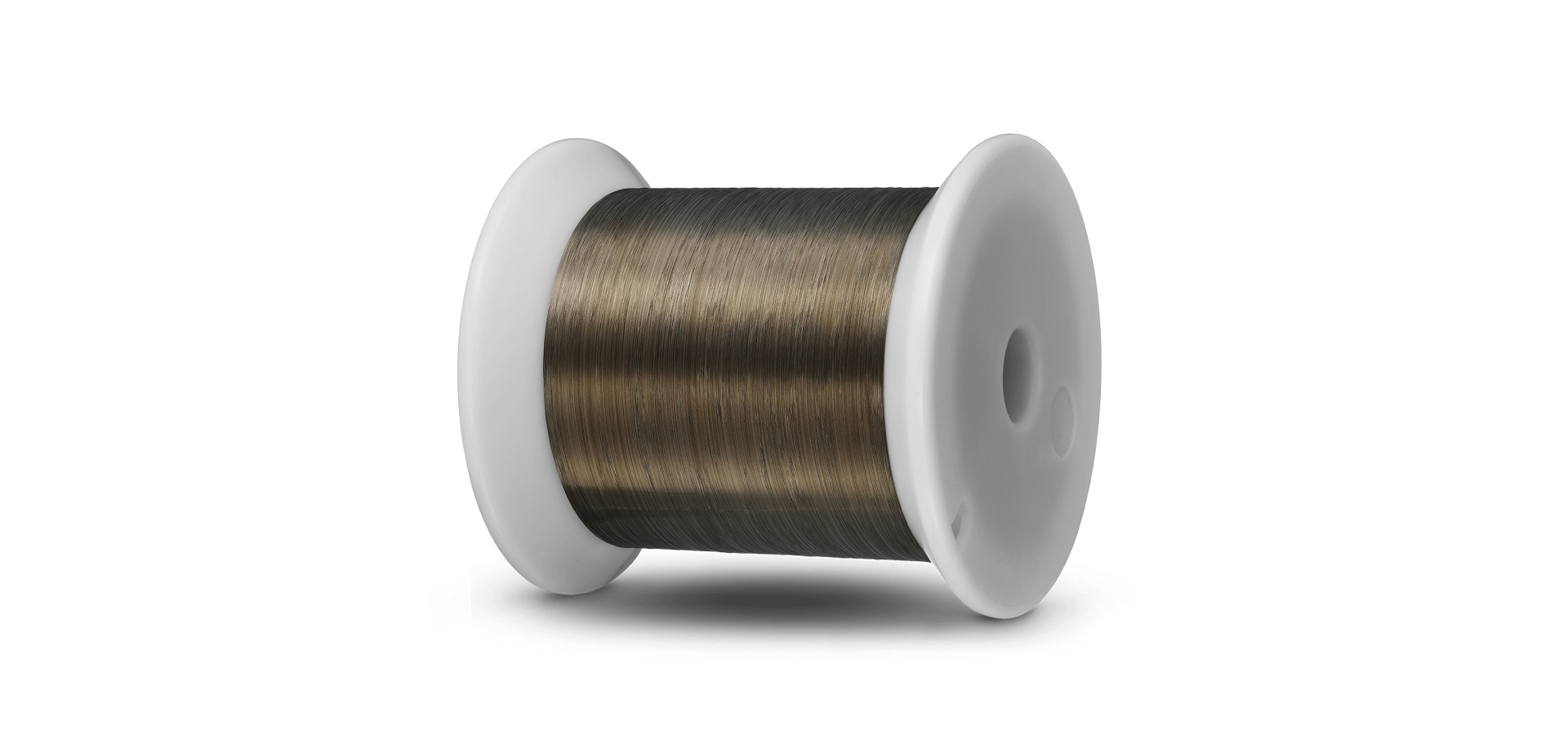
Two-Way Shape Memory Alloy Actuation Wire
Two-way Shape Memory Alloy (SMA) Actuation Wire, Autonomous Two-way 4%, High Phase Transition Temperature, Long Fatigue Life, Fast Electro-Thermal Response.
Technical Parameters:
Phase transition temperature: As ≈ 80°C;
Two-way shape recovery strain: ε₀ ≈ 4%;
Fatigue life at σᴿ = 172 MPa: N ≥ 1 million cycles;
Available diameters (φ mm): 0.025 / 0.050 / 0.075 / 0.100 / 0.150 / 0.200 / 0.300 / 0.400 / 0.500 (customized upon request).
Technical Advantages
-
Autonomous Two-way Memory Effect (4%)
Reversible strain without external load, simplifying actuator design. Ideal for high-frequency reciprocating motion (e.g., microrobotic joints, valve control). -
High-Temperature Phase Transition (As ≈ 80°C)
Suitable for elevated-temperature environments (e.g., automotive, aerospace thermal management). -
Exceptional Fatigue Life (≥1M cycles at 172 MPa)
Reliable for long-term dynamic applications (e.g., industrial actuators). -
Rapid Electro-Thermal Response
Millisecond-scale actuation in thin wires (e.g., φ0.025 mm), ideal for medical devices (e.g., endoscopic tools) or microsensors.
Selection & Usage Guidelines
-
Diameter Selection
Ultra-thin (φ0.025–0.1 mm): MEMS, medical catheters (low-voltage drive required).
Standard (φ0.15–0.5 mm): Industrial actuators, biomimetic robots (balance force output and durability).
-
Actuation Design
Pulsed current heating + passive cooling; thermal coatings recommended for faster response.
For high-temperature use, ensure ambient temperature < Af (assumed ≈100°C).
-
Fatigue Optimization
Operate below 172 MPa for extended lifespan; pre-straining may enhance cyclic stability.
-
Potential Applications
Aerospace: Hatch mechanisms, solar array deployment.
Medical: Foldable surgical tools, dynamic stents (biocompatible coating required).
Energy: Solar tracker fine-adjustment systems.